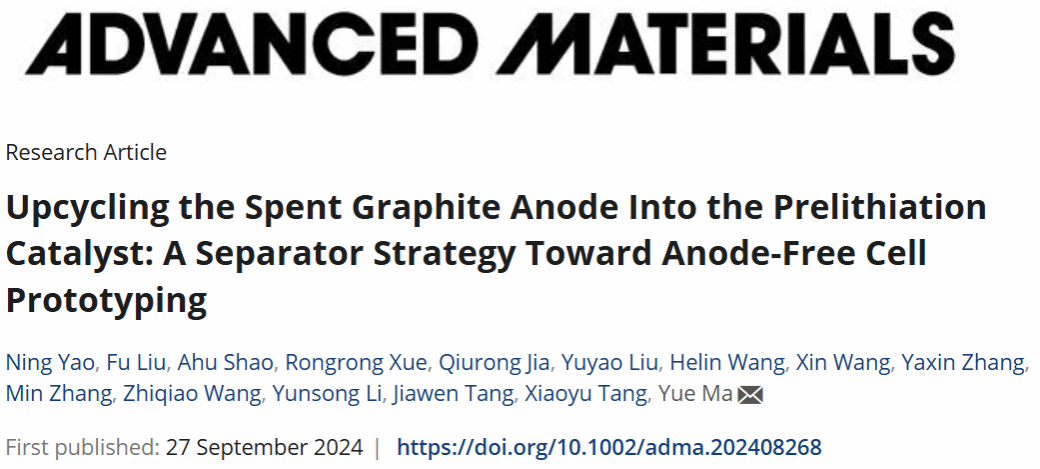
论文链接:https://doi.org/10.1002/adma.202408268
Research Background
The substantial market share of lithium-ion batteries necessitates the development of sustainable recycling strategies. To date, while efforts have been made to extract metals (such as lithium, nickel, and cobalt) from layered metal oxides (LiMxO2) or lithium iron phosphate (LFP) cathodes using complex chemical processes, the challenge remains to directly and efficiently recycle and regenerate cathodes without damaging the material structure or reconstructing the battery. Furthermore, the demands for high-value development of retired anodes in the "net-zero" era have also increased, prompting the need to fully utilize the structural characteristics induced by lithium to achieve an upgraded recycling of waste graphite, thereby driving the low-carbon transformation of the lithium battery manufacturing ecosystem.
Research Overview
Based on the above research background, this work proposes an "integrated closed-loop recycling" strategy. By fine-tuning the interlayer spacing and defect concentration, waste graphite is upgraded to a prelithiation catalyst, specifically few-layer graphene flakes (FGF). Specifically, the defect-catalyzed structure within the FGF facilitates the efficient release of Li⁺ from the Li5FeO4 reagent. Furthermore, through hydrophobic molecular modification and ultrathin thickness control, an air-stable separator based on waste graphite achieves a lithium ion utilization rate of 98%. During a complete electrochemical cycle, this strategy can provide customized lithium supplementation capacity (up to 0.51 mAh cm⁻⟡) for retired lithium iron phosphate (DLFP) without requiring any cumbersome electrode processing or stringent environmental control. Additionally, this separator strategy adjusts the interfacial chemical properties in anode-free batteries. The assembled LFP||FGF/LFO@6FAP-PP||FGF-Cu soft-pack battery (1.5 Ah) exhibits superior cycling durability (73.1% capacity retention after 200 cycles), an energy density of 386.6 Wh kg⁻¹, and a peak output power of 1159.8 W kg⁻¹. This article, titled “Upcycling the Spent Graphite Anode into the Prelithiation Catalyst: A Separator Strategy toward Anode-free Cell Prototyping,” was published in the international journal Advanced Materials (Impact Factor = 27.4). The first author is Yao Ning, a master's student from the Nano Energy Materials Research Center of the School of Materials Science, with Professor Ma Yue as the corresponding author, and Northwestern Polytechnical University as the primary affiliation.
Research Highlights
1.Hydrophobic Prelithiation Separator: Through hydrophobic molecular modification, the prelithiation separator demonstrates excellent moisture resistance (30% relative humidity for 6 h ), significantly reducing the manufacturing costs of batteries.
2.Catalytic Mechanism of FGF in Improving Prelithiation Efficiency: DFT theoretical calculations and experimental data elucidate the catalytic role of FGF in lowering the delithiation energy barrier of lithium supplementation reagents.
3.Regeneration Mechanism of Waste LFP: In situ XRD real-time monitoring during the electrochemical process shows the phase transition of delithiated LFP electrodes from a biphasic structure (FePO4, LiFePO4) to a pure LiFePO4 phase, confirming the in-situ repair of the DLFP structure by the prelithiation separator.
图文导读
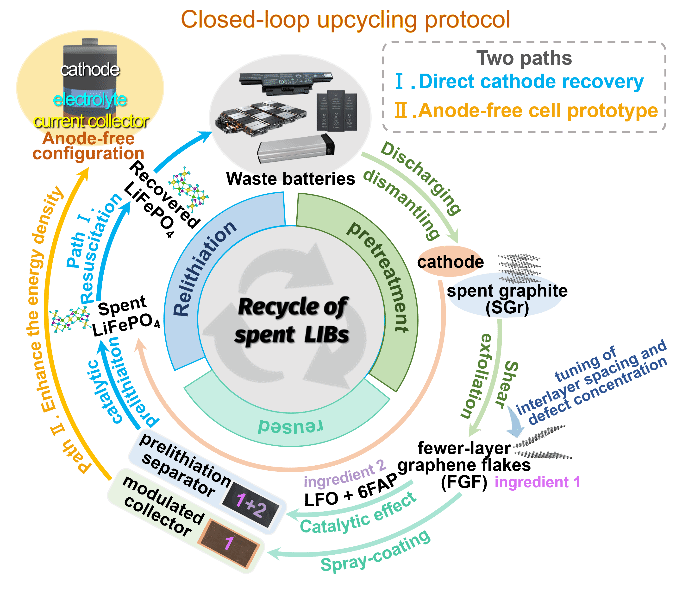
图1. 废旧锂离子电池闭环回收路线。路径Ⅰ:将SGr回收升级为预锂化催化剂FGF,构建空气稳定型预锂化隔膜,对缺锂DLFP正极进行原位修复;路径Ⅱ:将商业LFP匹配改性FGF-Cu,在预锂化隔膜辅助下构建高能量anode-free电池。
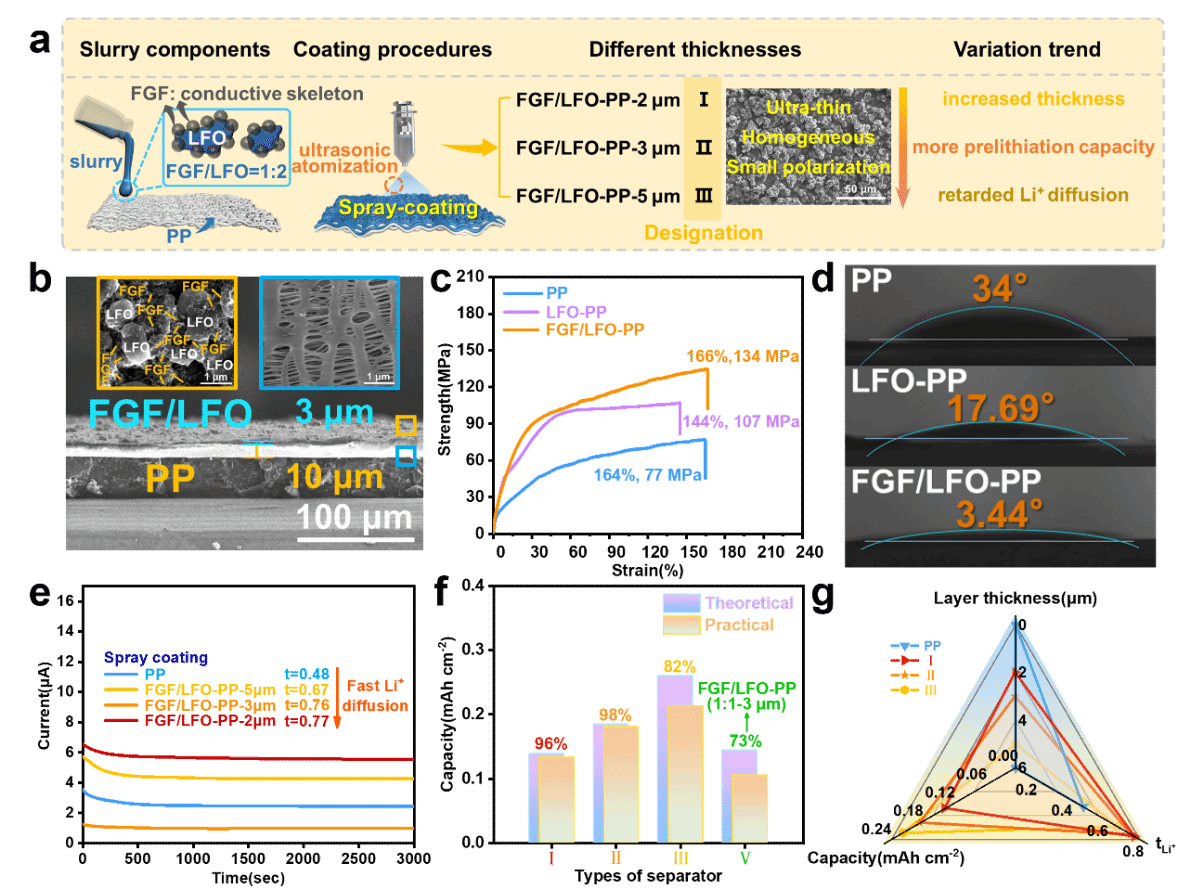
图2.(a)将预锂化复合材料(FGF/LFO)喷涂在PP隔膜上的过程示意图。涂层厚度分别为2 μm、3 μm和5 μm的隔膜被命名为样品Ⅰ、Ⅱ和Ⅲ。(b)II型预锂化隔膜的横截面SEM图像。(c,d)PP、LFO-PP和FGF/LFO-PP预锂化隔膜的拉伸强度和电解液润湿性能。(e,f)采用超声喷涂方式制备的不同类型预锂化隔膜的锂离子迁移数测试、补锂面容量和容量利用率。(g)不同类型预锂化隔膜的雷达图。
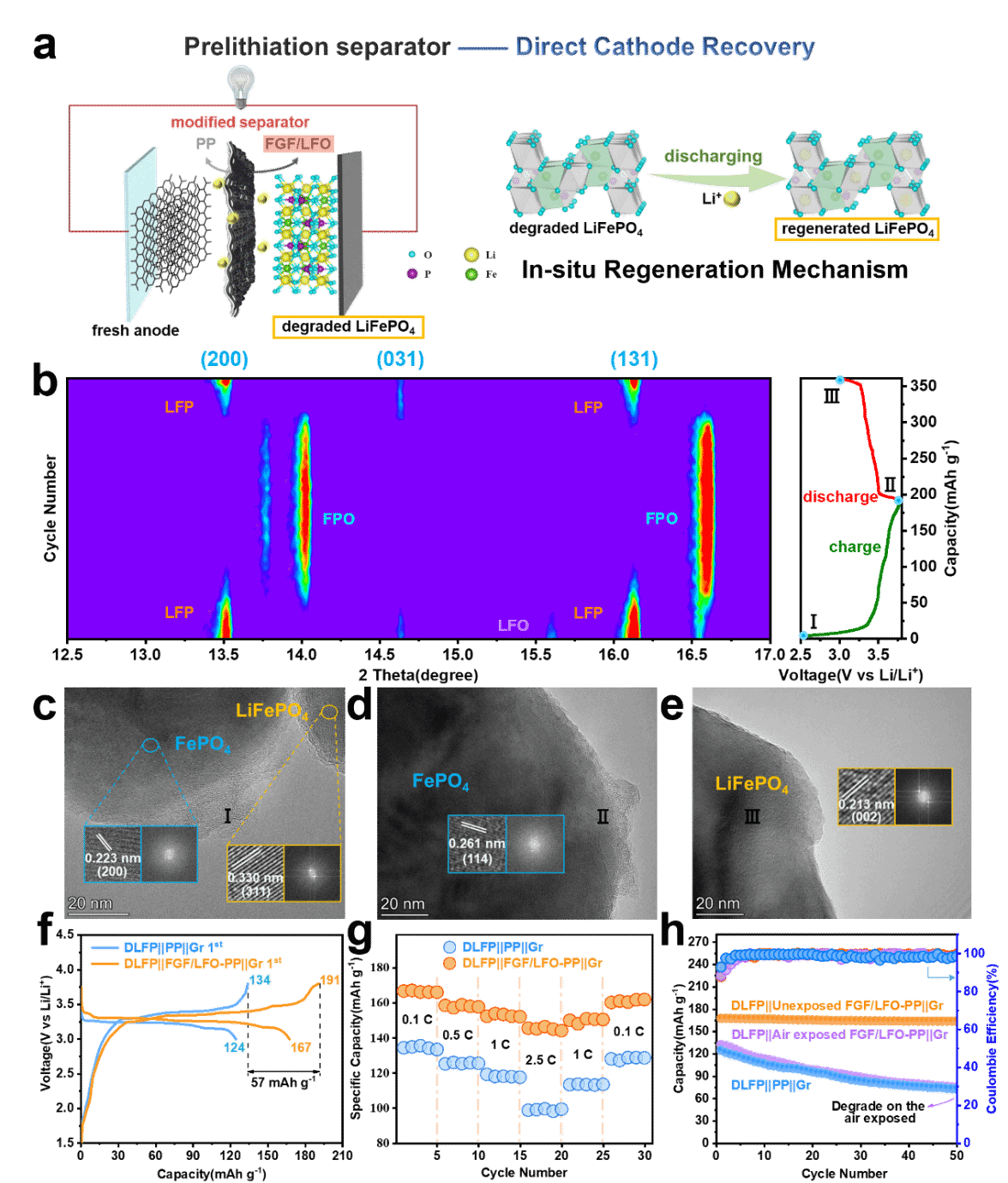
图3.(a)基于FGF/LFO-PP预锂化隔膜修复DLFP的再生机理示意图。(b)DLFP在0.1 C倍率下初始充放电过程中的原位XRD图谱及充放电曲线。(c-e)DLFP颗粒在首圈充放电曲线中三种不同状态下对应的TEM图像。(f,g)DLFP和再生LFP(RLFP)的首圈充放电曲线和倍率性能(h)DLFP再生电池在1 C下的循环性能(30% RH,6h)。
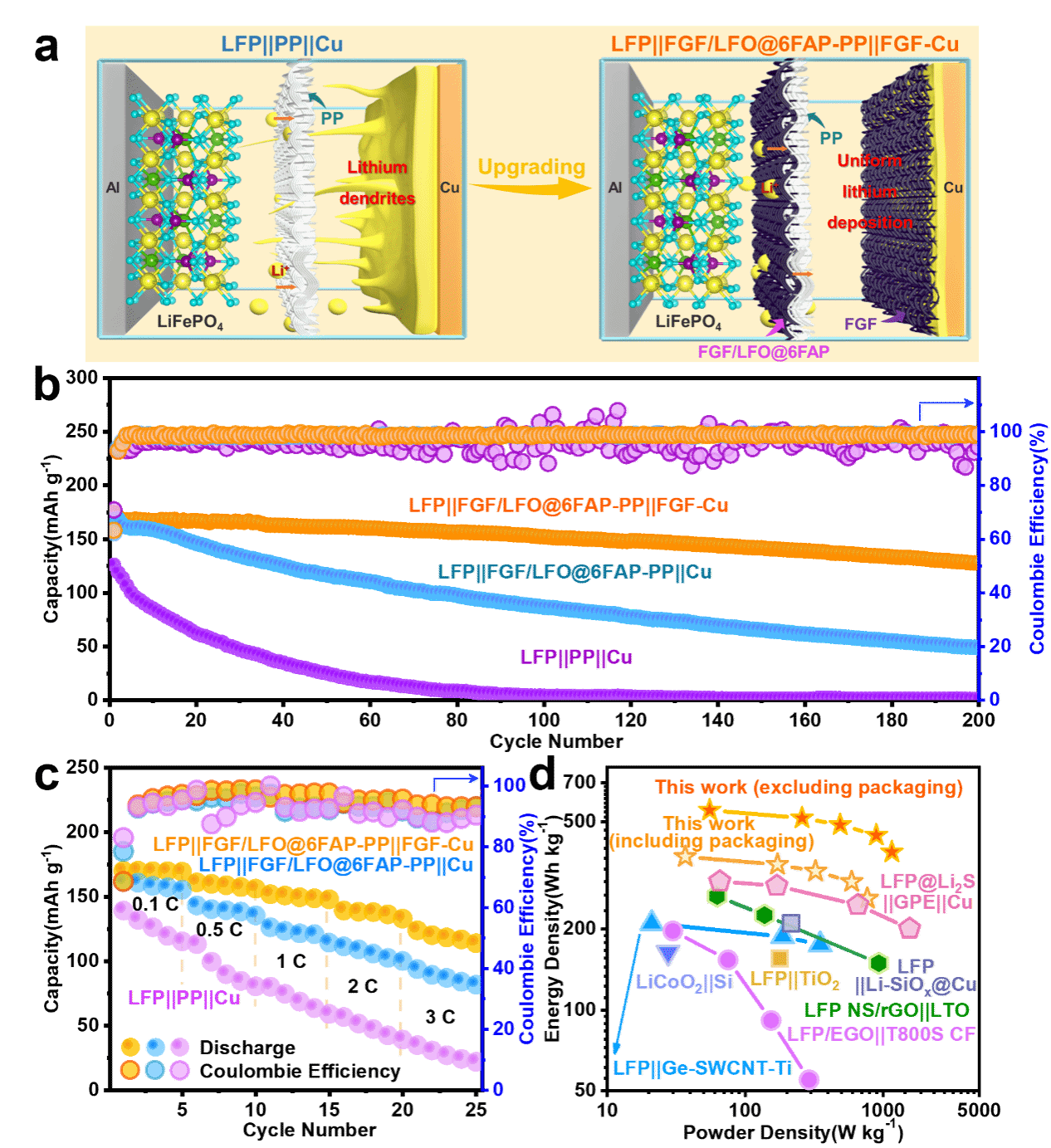
图4.(a)LFP||PP||Cu和LFP||FGF/LFO@6FAP-PP||FGF-Cu电池构型的示意图。(b,c)三种无负极电池(LFP||PP||Cu、LFP||FGF/LFO@6FAP-PP||Cu及LFP||FGF/LFO@6FAP-PP||FGF-Cu模型)的循环稳定性和倍率性能。(d)LFP||FGF/LFO@6FAP-PP||FGF-Cu无负极电池模型基于活性物质质量和整个电池质量的Ragone图。
Conclusion
This work proposes a prelithiation separator strategy based on waste graphite. By adjusting the interlayer spacing and defect structures within the waste graphite, the waste graphite anode can serve as a catalyst for the prelithiation reagent LFO. After thickness optimization and waterproof modification, the LFO/6FAP@FGF-PP prelithiation separator can provide sufficient lithium supplementation surface capacity (0.18 mAh cm⁻⟡) and achieve in situ repair of retired lithium iron phosphate electrodes during electrochemical cycling, all without the need for cumbersome electrode processing or strict environmental controls. Notably, this prelithiation separator strategy also stabilizes the interfacial chemical properties of the battery, allowing for the construction of an anode-free battery that features both high energy density and cycling durability using commercially available LFP paired with modified FGF-Cu current collectors. This closed-loop recycling strategy, focused on structural characteristics, upgrades waste graphite into a high-value catalytic additive, enabling efficient repair of lithium-deficient electrodes. It not only promotes the sustainable development of the battery manufacturing supply chain but also achieves the design of high-energy, anode-free batteries from a more efficient perspective.
Corresponding Author Profile
Professor Ma Yue: Prof Ma works at the School of Materials Science at Northwestern Polytechnical University. He has led multiple projects funded by the National Natural Science Foundation, key projects in Shaanxi Province, and international cooperation and exchange initiatives. In recent years, he has published over 110 papers in journals such as Nature Communications, Advanced Materials, Chem, Energy & Environmental Science, Advanced Energy Materials, ACS Nano, Energy Storage Materials, and Nano Energy. His research focuses on the controllable preparation and interface modification methods of key materials for chemical power sources, in situ/online characterization techniques, and the analysis of the evolution mechanisms of surface/interface reactions.