1.Introduction
The 26th United Nations Climate Change Conference (COP26) advocated for the decarbonization of the aviation industry. Hydrogen energy, characterized by its green, pollution-free nature, high energy density, abundant availability, and diverse application markets, is regarded as a crucial energy source for the future development of aviation. Consequently, the advancement of hydrogen-fueled aircraft engines has attracted significant attention. Superalloys are currently the most widely used materials for the hot-end components of gas turbine engines. However, research on hydrogen-related superalloys has predominantly focused on nuclear energy applications, with limited studies addressing the actual service conditions of aerospace engines.
Superalloy components are typically subjected to alternating loads during service, and fatigue fracture is a common failure mode. Studies have shown that the presence of hydrogen reduces the fatigue life of materials. Due to the challenges associated with characterizing hydrogen, it is difficult to thoroughly investigate its impact on material deformation through conventional experiments. The use of crystal plasticity finite element (CPFE) methods allows for direct prediction of interactions between hydrogen and microstructural features such as dislocations and grain boundaries. Therefore, combining experimental approaches with hydrogen diffusion-coupled CPFE simulations to explore hydrogen-assisted fatigue crack growth behavior is of great significance for the development and application of alloys in future hydrogen-fueled aircraft engines.

2.Summary of Research Findings
Professor Jinshan Li’s group from the State Key Laboratory of Solidification Technology conducted an in-depth study on the effect of hydrogen atoms on the fatigue crack growth behavior of IN625 alloy, elucidating the mechanisms of hydrogen-assisted crack propagation and fatigue striation formation. In this study, IN625 alloy underwent hydrogen charging at 600℃ under a hydrogen pressure of 1.15 kgf/cm2 for 20 hours, followed by fatigue crack growth experiments under constant ΔP and constant ΔK conditions with varying fatigue loading frequencies. The fatigue crack growth rates were calculated using the compliance method, revealing the influence of hydrogen on the crack growth rate.
Fracture surface morphology and crack propagation paths were analyzed through SEM, EBSD, and ECCI characterization, clarifying the evolution of plastic deformation and fatigue striations. CPFE simulations, incorporating hydrogen diffusion effects, were employed to predicted the accumulation of damage at the crack tip under different loading conditions. These simulations identified the role of dislocation slip in fatigue crack growth under hydrogen-charged conditions, shedding light on the hydrogen-assisted fatigue crack growth mechanisms of IN625. The findings provide valuable theoretical guidance for the microstructural design and application of hydrogen-related superalloys.
The research, titled “Experimental and Crystal Plasticity Study on Hydrogen-Assisted Fatigue Crack Growth Behavior of IN625 Superalloy” has been published in the leading corrosion journal Corrosion Science (DOI: 10.1016/j.corsci.2024.112480). The corresponding authors are Professor Jinshan Li and Professor Bin Tang from the State Key Laboratory of Solidification Technology, and the first author is Ph.D candidate Kaidi Li. This work was supported by the National Science and Technology Major Project (J2019-VI-0023-0140).
3.Graphical Overview
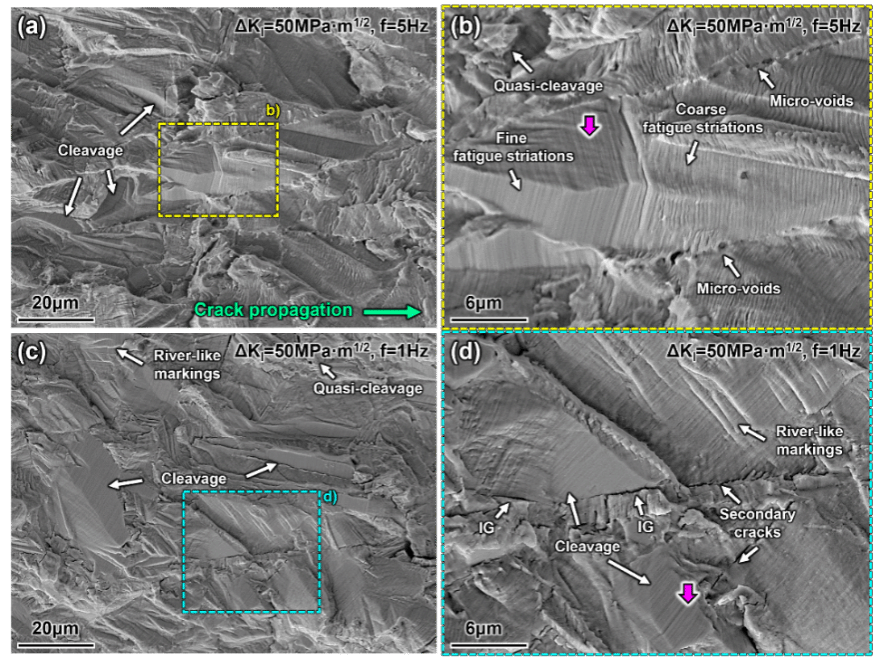
Fig. 1 Fracture morphologies of hydrogen-charged samples under 5 Hz and 1 Hz loading frequencies at different stress intensity factor ranges.
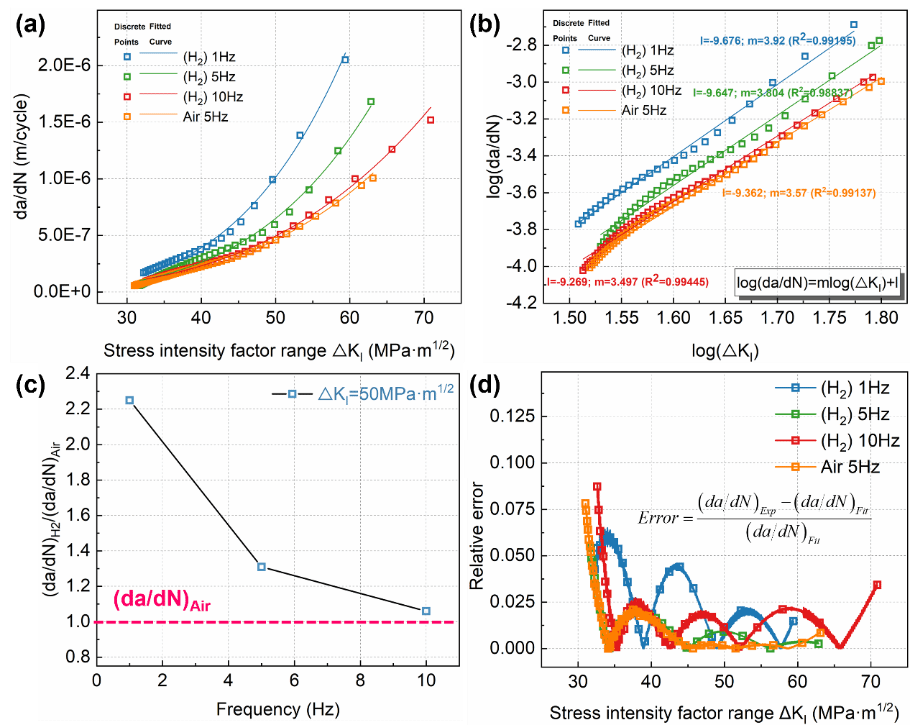
Fig. 2 Fatigue crack growth rate curves and error curves.
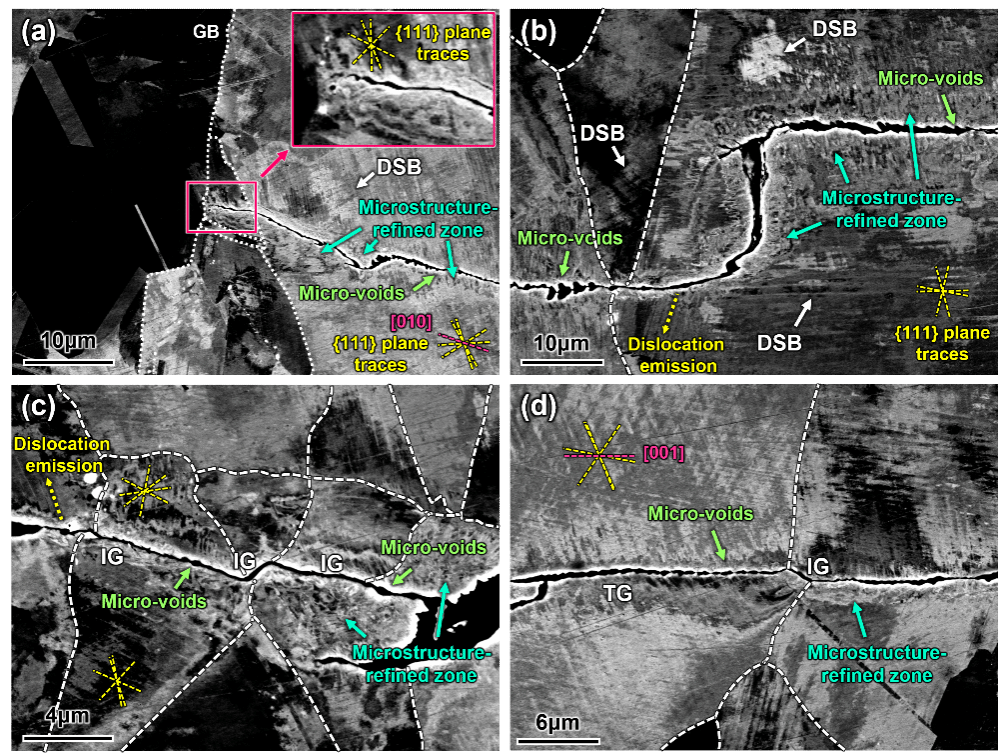
Fig. 3 ECC images of crack propagation paths in hydrogen-charged samples.
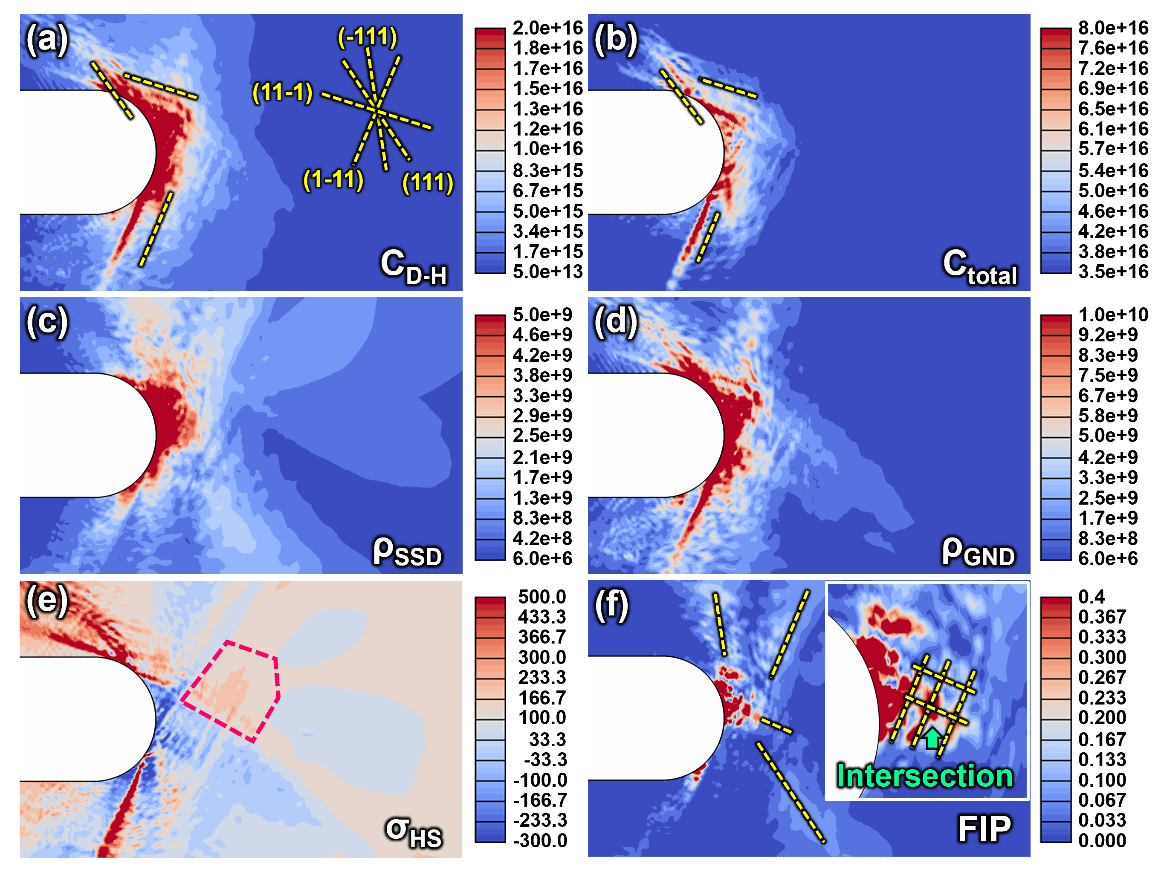
Fig. 4 Contour maps of hydrogen concentration and damage variables at the crack tip.
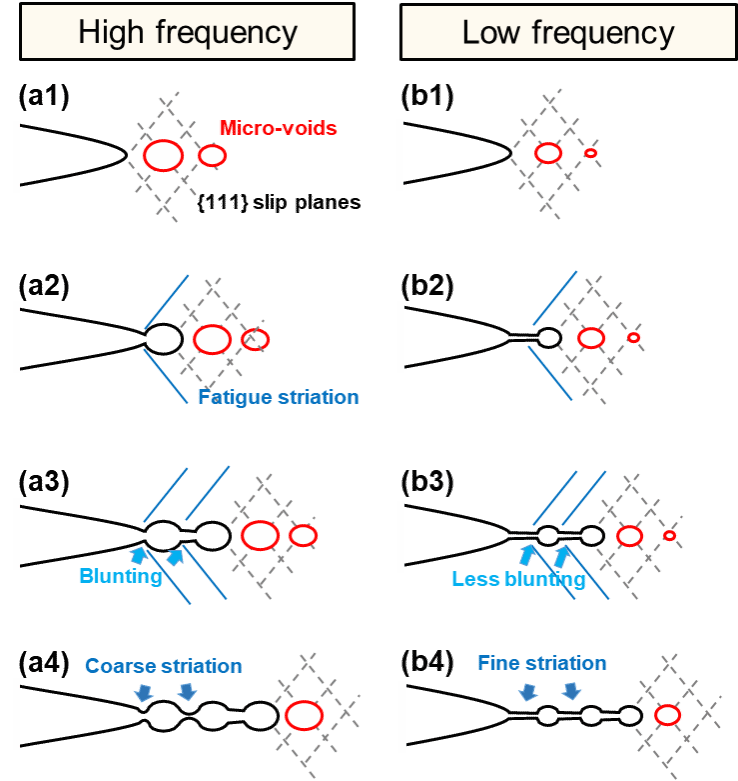
Fig. 5 Schematic diagram of fatigue striation formation mechanism under hydrogen-charged conditions.